Predicción del momento óptimo para el mantenimiento
Lo que parecía ciencia ficción hace relativamente poco, actualmente ya es una realidad en las nuevas soluciones disponibles de Schaeffler: el mantenimiento predictivo. Los diagnósticos automáticos de rodamientos y los cálculos de la duración de vida útil residual de los rodamientos son componentes importantes de la Industria 4.0.
Diagnóstico automático de rodamientos
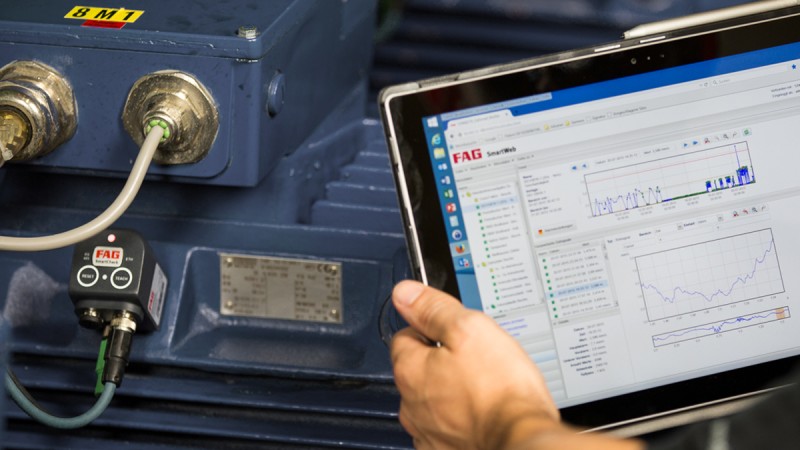
En la Feria de Hannover 2016, Schaeffler presentó nuevas soluciones de mantenimiento predictivo que proporcionan información sobre la futura condición de sus máquinas a los operadores de maquinaria. El mantenimiento predictivo no solo permite optimizar la utilización de la capacidad productiva de las plantas, sino también programar los intervalos de mantenimiento.
Un requisito previo importante para el mantenimiento predictivo es el diagnóstico automático de los rodamientos, una función que se utiliza, por ejemplo, en las unidades de motor y transmisión. Estas unidades no solo se utilizan en máquinas-herramienta, sino también en cintas transportadoras, prensas e incluso cilindros de acerías.
Puesto que los accionamientos de las máquinas funcionan prácticamente sin interrupción, requieren un mantenimiento intensivo para prevenir las paradas no programadas de la producción. Por este motivo es tan importante que los operadores conozcan en todo momento la condición de los componentes de accionamiento, y por qué los rodamientos son particularmente importantes como elementos centrales de las máquinas.
La nueva generación del sistema de diagnóstico FAG SmartCheck representa ahora un paso más para Schaeffler. Además de identificar la amenaza de daños, desgaste e irregularidades en los rodamientos como desequilibrios y errores de alineación basándose en los cambios en el patrón de vibración, el sistema también cuenta con una conexión al entorno cloud. El sistema crea un diagnóstico automático en el entorno cloud a partir de los datos brutos proporcionados por el FAG SmartCheck y de datos adicionales procedentes, por ejemplo, de la unidad de mando de la máquina.
Cálculo de la duración residual de vida útil de los rodamientos
Los sistemas como el FAG SmartCheck se denominan sistemas de "Condition Monitoring". Éstos permiten el diagnóstico automático de la condición de los rodamientos y los componentes de la maquinaria. Además, el almacenamiento de los datos en el entorno cloud también permite utilizarlos para otros cálculos, como las simulaciones del tren de potencia y los rodamientos por lo que respecta a su resistencia estática y dinámica.
Utilizando los espectros de carga reales recopilados durante el funcionamiento, Schaeffler puede calcular, por encargo del cliente, continuamente la duración de vida útil residual de los rodamientos a intervalos libremente definidos. La herramienta de cálculo BEARINX de Schaeffler recupera los datos del entorno cloud. Los clientes podrán consultar la duración de vida útil residual de cada rodamiento de la máquina en un dispositivo móvil conectado a Internet.
La solución de Schaeffler se basa en tres elementos centrales:
- Un sistema adecuado de sensores que recopila datos de carga fiables para la máquina y sus rodamientos.
- Modelos de simulación que calculan la duración de vida útil residual basándose en las dimensiones de la máquina y las cargas reales.
- Una plataforma de software que permite que el cliente acceda a los cálculos y obtenga información individualizada sobre su máquina.
Planificación del intervalo de mantenimiento óptimo
"Esto permite optimizar, por ejemplo, la programación de la producción. La producción se puede aumentar si lo requiere la situación de los pedidos y si se dispone de capacidad de maquinaria suficiente. Por otra parte, la producción se puede reducir si hay menos pedidos pendientes y se puede adaptar a un intervalo específico de mantenimiento".
De esta manera, el mantenimiento de la maquinaria de producción puede realizarse en función de las condiciones de carga y de acuerdo con los requerimientos en lugar de basarse en intervalos específicos y averías graves. Proceder así proporciona numerosos beneficios, entre ellos el aumento de la productividad gracias a la correlación entre el nivel de utilización de la capacidad de producción y la condición de los componentes de las máquinas. Además, las piezas de recambio se pueden pedir 'just-in-time', lo que reduce los costes de almacenamiento. Por último, pero no por ello menos importante, se puede reducir el total de costes operativos gracias a la utilización optimizada de los intervalos de mantenimiento. Incluso en caso de daños incipientes en un rodamiento, el mantenimiento predictivo también puede ayudar: Si el operador sabe durante cuánto tiempo continuará funcionando un rodamiento, puede tomar una decisión válida sobre si debe continuar o no la producción.
De proyectos a producción en serie
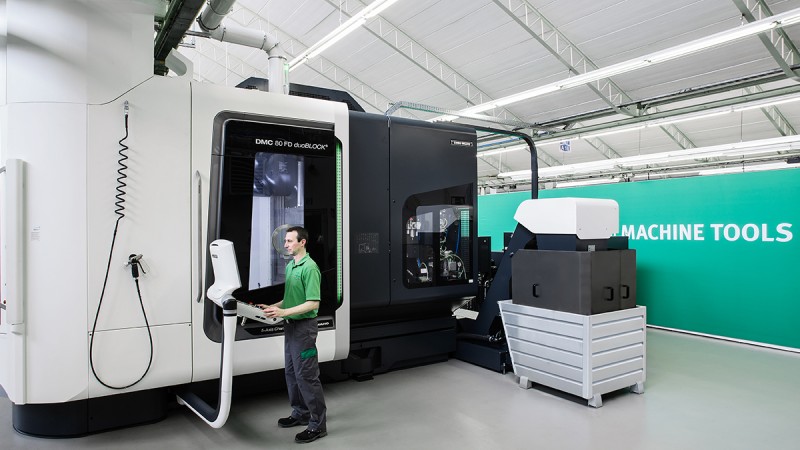
El objetivo de Schaeffler es crear soluciones completas estandarizadas a partir de los enfoques tecnológicos ya desarrollados. "Tenemos la tecnología de sensores, los modelos de cálculo y la plataforma de software, y nuestros desarrollos están a punto de hacer posible la producción masiva", afirma el Dr. Keßler.
Ya se han implementado las primeras aplicaciones piloto, entre ellas la "Máquina-herramienta 4.0" ubicada en la planta de Schaeffler en Höchstadt, que está totalmente conectada y enlazada con el entorno cloud y se utiliza para la producción masiva de rodamientos de alta precisión. El mantenimiento predictivo también puede ser de gran utilidad en otras aplicaciones industriales, entre ellas los aerogeneradores de alta mar: "Si existe la posibilidad de calcular con antelación si la multiplicadora de un aerogenerador aguantará el próximo período de fuertes vientos entre septiembre y marzo, el operador podrá tomar una decisión basándose en las necesidades sobre si las tareas de mantenimiento deben llevarse a cabo en la multiplicadora antes de que empiece el invierno", explica el Dr. Keßler.
Al realizar las tareas de mantenimiento según las condiciones reales de funcionamiento, Schaeffler marca el inicio de un cambio de paradigma en la ingeniería mecánica. En una segunda etapa, los espectros de carga medidos se podrán utilizar para rediseñar y reconfigurar por completo tanto los componentes individuales como las máquinas enteras para adaptarlos a las condiciones de carga pertinentes.